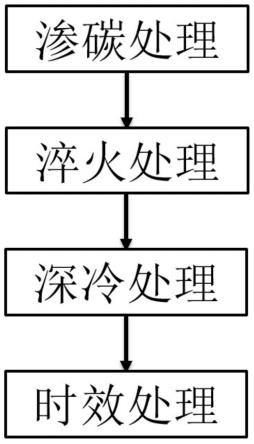
一种机床主轴20crmnti钢的深冷处理工艺
技术领域
1.本发明涉及金属材料热处理领域,特别涉及一种机床主轴用20crmnti钢的深冷处理工艺。
背景技术:2.近年来,随着航空航天、国防高尖端技术以及民用高技术产品的迅速发展,超精密机床已经成为必不可少的装备。主轴是超精密机床的重要部件,主轴的不稳定将直接影响机床的整体性能。
3.目前,国内精密机床主轴所用材料主要为20crmnti,其制造过程中热处理工艺主要为渗碳处理、淬火处理、时效处理。通过目前的热处理工艺制造的20crmnti主轴,其表层为坚硬的渗碳层,心部为具有良好综合力学性能的马氏体或贝氏体组织。可见,机床主轴的组织中主要含有马氏体、贝氏体、残余奥氏体等,这些组织及淬火产生的残余应力对主轴的力学性能有着重要的影响。然而,目前生产的主轴往往只关注表面硬度,未关注心部组织及力学性能。通过渗碳+淬火+时效处理后表面硬度能满足生产要求,但是心部的韧性不足会导致主轴在服役过程中疲劳寿命较低,此外,组织中的残余奥氏体在服役过程中会发生分解,导致主轴变形,影响主轴的精度寿命。因此,需要优化机床主轴用20crmnti钢热处理工艺,制备出高强度、高冲击韧性、组织稳定性好的主轴产品,从而提高机床主轴的服役寿命。
技术实现要素:4.鉴于此,本发明的目的在于提供一种机床主轴用20crmnti钢的深冷处理工艺,旨在克服现有主轴心部因韧性不足而导致主轴在服役过程中疲劳寿命降低的缺陷,同时解决现有主轴心部组织中因残余奥氏体在服役过程中会发生分解,导致主轴变形,影响主轴精度寿命的问题。
5.为了达到上述发明目的,进而采取的技术方案如下:
6.一种机床主轴用20crmnti钢的深冷处理工艺,包括以下步骤:
7.渗碳处理:对20crmnti钢的机床主轴表面进行渗碳处理;其中,渗碳后机床主轴表面含碳量为0.8-1.2wt%,渗碳层深度为1.2-2.0mm;
8.淬火处理:将渗碳后的机床主轴淬火处理后油冷至室温;
9.深冷处理:在淬火结束后的6h内,对完成淬火的机床主轴进行深冷处理,降温速率为50-70℃/h,深冷温度为-60~-100℃,保温2-4h后取出空冷恢复至室温;
10.时效处理:将深冷处理后的机床主轴进行精加工后,进行时效处理,加热速率为50-70℃/h,时效温度为190~210℃,保温6-12h后空冷至室温。
11.进一步的,所述渗碳处理采用强渗和扩散工艺对机床主轴表面渗碳,渗碳后机床主轴表面含碳量为0.8-1.2wt%,渗碳层深度为1.2-2.0mm;
12.较进一步的,所述淬火处理的加热温度为850
±
15℃,保温1-4h,出炉后,将机床主轴投入淬火油中冷却至室温,其中,淬火油的油温为50
±
5℃。
13.更进一步的,经深冷处理工艺后的机床主轴的表面组织为针状的马氏体,心部组织为贝氏体或马氏体。
14.本发明与现有技术相比,具有以下有益效果:
15.本发明采用的渗碳处理+淬火处理+深冷处理+时效处理,通过深冷处理,促进残余奥氏体的分解,这样就能将残余奥氏体转变为马氏体,提高主轴表面的硬度,而心部组织中残余的奥氏体也能充分地进行转变,从而提高主轴心部的强韧性,减小服役过程变形的可能性,从而提高服役寿命。
附图说明
16.为了更清楚地说明本发明实施例或现有技术中的技术方案,下面将对实施例或现有技术描述中所需要使用的附图作简单地介绍,显而易见地,下面描述中的附图仅仅是本发明的一些实施例,对于本领域普通技术人员来讲,在不付出创造性劳动性的前提下,还可以根据这些附图获得其他的附图。
17.图1为本发明的深冷处理工艺流程图;
18.图2为本发明实施例1热处理后表面金相组织图;
19.图3为本发明实施例1热处理后心部金相组织图;
20.图4为本发明实施例1和对比例试样的xrd测试结果;
21.图5为本发明实施例1和对比例试样的残余奥氏体检测结果。
具体实施方式
22.下面将结合本发明实施例中的附图,对本发明实施例中的技术方案进行清楚、完整地描述,显然,所描述的实施例仅仅是本发明一部分实施例,而不是全部的实施例。基于本发明中的实施例,本领域普通技术人员在没有做出创造性劳动前提下所获得的所有其他实施例,都属于本发明保护的范围。
23.由于目前,国内的精密机床主轴的组织主要为马氏体、贝氏体和残余奥氏体等,尤其是残余奥氏体在服役过程中会发生分解,导致主轴变形;同时心部的韧性也存在不同,导致主轴服役过程中疲劳寿命较低。
24.所以,申请人的研发目的在于如何优化热处理工艺,以分解机床主轴心部组织中的残余奥氏体,以及改变热处理工艺后,以增加心部组织的韧性。
25.因此,申请人基于上述的研发思路,经过创造性的劳动,将原来的热处理工艺“渗碳+淬火+时效处理”优化成本技术中的“渗碳+淬火+深冷处理+时效处理”,也就得到本发明的技术方案,内容如下:
26.一种机床主轴用20crmnti钢的深冷处理工艺,包括以下步骤:
27.渗碳处理:对20crmnti钢的机床主轴表面进行渗碳处理;其中,渗碳处理采用强渗和扩散工艺对机床主轴表面渗碳,渗碳后机床主轴表面含碳量为0.8-1.2wt%,渗碳层深度为1.2-2.0mm;
28.淬火处理:将渗碳后的机床主轴淬火处理后油冷至室温;其中,淬火处理的加热温度为850
±
15℃,保温1-4h,出炉后,将机床主轴投入淬火油中冷却至室温,其中,淬火油的油温为50℃
±
5℃。
29.深冷处理:在淬火结束后的6h内,对完成淬火的机床主轴进行深冷处理,降温速率为50-70℃/h,深冷温度为-60~-100℃,保温2-4h后取出空冷恢复至室温。
30.时效处理:将深冷处理后的机床主轴进行精加工后,进行时效处理,加热速率为50-70℃/h,时效温度为190~210℃,保温6-12h后空冷至室温。
31.本发明的设计思想和原理如下:机床主轴传统热处理为渗碳处理+淬火处理+时效处理,由于渗碳处理会使材料表面增碳,导致主轴材料表面含碳量高,在随后的淬火过程中材料表面及心部产生较多的残余奥氏体,残余奥氏体经过时效处理后并不能完全分解,而是在加工及服役过程中缓慢分解。而残余奥氏体在加工及服役过程分解会导致材料内部应力状态发生变化,从而造成主轴变形,减少服役寿命。本发明采用的渗碳处理+淬火处理+深冷处理+时效处理,通过深冷处理,促进残余奥氏体的分解,这样就能将残余奥氏体转变为马氏体,提高主轴表面的硬度,而心部组织中残余的奥氏体也能充分地进行转变,从而提高主轴心部的强韧性,减小服役过程变形的可能性,从而提高服役寿命。
32.鉴于上述公开的技术方案,本发明的具体实施过程如下:
33.实施例1
34.(1)渗碳处理:采用强渗和扩散工艺对20crmnti主轴进行表面渗碳,渗碳温度为925℃,强渗碳势为1.20%,渗碳时间为7h,扩散的碳势为0.9%,扩散时间为3.5h。
35.(2)淬火处理:渗碳完成后,随炉冷却至850℃,出炉油冷至室温,油温为50℃。
36.(3)深冷处理:将淬火后的20crmnti主轴在淬火结束2h后,放入深冷炉,进行深冷处理,降温速率为60℃/h,深冷温度为-80℃,保温2h后取出空冷恢复至室温;
37.(4)时效处理:深冷处理后的20crmnti主轴进行精加工处理后,放入时效热处理炉中进行时效处理,加热温度为50℃/h,时效温度为200℃,保温时间为8h,随后出炉空冷至室温。
38.本实施例经过最终处理后,对表面和心部分别进行含碳量检测、组织观察和洛氏硬度测试等,在心部取样加工成标准室温拉伸试样和夏比v口冲击试样。测试结果表明,经过本实施例的热处理后,20crmnti主轴的表面含碳量约为1.05wt%,渗碳层厚度为1.8mm,表面硬度达到62hrc;心部材料抗拉强度达到1205mpa,室温冲击功达到115j。试样的表面和心部组织如图2、3所示,可以看出经过本发明处理后的表面组织主要为针状马氏体,心部为低温时效处理的贝氏体和马氏体的混合组织。
39.实施例2
40.(1)渗碳处理:采用强渗和扩散工艺对20crmnti主轴进行表面渗碳,渗碳温度为925℃,强渗碳势为1.10%,渗碳时间为6h,扩散的碳势为0.9%,扩散时间为4h。
41.(2)淬火处理:渗碳完成后,随炉冷却至860℃,出炉油冷至室温,油温为55℃。
42.(3)深冷处理:将淬火后的20crmnti主轴在淬火结束3h后,放入深冷炉,进行深冷处理,降温速率为50℃/h,深冷温度为-90℃,保温2h后取出空冷恢复至室温;
43.(4)时效处理:深冷处理后的20crmnti主轴进行精加工处理后,放入时效热处理炉中进行时效处理,加热温度为50℃/h,时效温度为200℃,保温时间为12h,随后出炉空冷至室温。
44.本实施例经过最终处理后,对表面进行含碳量检测和洛氏硬度测试,在心部取样加工成标准室温拉伸试样和夏比v口冲击试样。测试结果表明,经过本实施例的热处理后,
20crmnti主轴的表面含碳量约为0.85wt%,渗碳层厚度为1.35mm,表面硬度达到63hrc;心部材料抗拉强度达到1195mpa,室温冲击功达到107j。
45.实施例3
46.(1)渗碳处理:采用强渗和扩散工艺对20crmnti主轴进行表面渗碳,渗碳温度为920℃,强渗碳势为1.25%,渗碳时间为8h,扩散的碳势为0.9%,扩散时间为4h。
47.(2)淬火处理:渗碳完成后,随炉冷却至850℃,出炉油冷至室温,油温为50℃。
48.(3)深冷处理:将淬火后的20crmnti主轴在淬火结束2h后,放入深冷炉,进行深冷处理,降温速率为50℃/h,深冷温度为-60℃,保温2h后取出空冷恢复至室温;
49.(4)时效处理:深冷处理后的20crmnti主轴进行精加工处理后,放入时效热处理炉中进行时效处理,加热温度为50℃/h,时效温度为200℃,保温时间为8h,随后出炉空冷至室温。
50.本实施例经过最终处理后,对表面进行含碳量检测和洛氏硬度测试,在心部取样加工成标准室温拉伸试样和夏比v口冲击试样。测试结果表明,经过本实施例的热处理后,20crmnti主轴的表面含碳量约为1.00wt%,表面渗碳层厚度为1.6mm,表面硬度达到62hrc;心部材料抗拉强度达到1175mpa,室温冲击功达到95j。
51.实施例4
52.(1)渗碳处理:采用强渗和扩散工艺对20crmnti主轴进行表面渗碳,渗碳温度为925℃,强渗碳势为1.20%,渗碳时间为10h,扩散的碳势为0.9%,扩散时间为4h。
53.(2)淬火处理:渗碳完成后,随炉冷却至850℃,出炉油冷至室温,油温为50℃。
54.(3)深冷处理:将淬火后的20crmnti主轴在淬火结束2h后,放入深冷炉,进行深冷处理,降温速率为60℃/h,深冷温度为-100℃,保温2h后取出空冷恢复至室温;
55.(4)时效处理:深冷处理后的20crmnti主轴进行精加工处理后,放入时效热处理炉中进行时效处理,加热温度为50℃/h,时效温度为200℃,保温时间为8h,随后出炉空冷至室温。
56.本实施例经过最终处理后,对表面进行含碳量检测和洛氏硬度测试,在心部取样加工成标准室温拉伸试样和夏比v口冲击试样。测试结果表明,经过本实施例的热处理后,20crmnti主轴的表面含碳量约为1.02wt%,表面渗碳层厚度为1.70mm,表面硬度达到62.5hrc;心部材料抗拉强度达到1210mpa,室温冲击功达到110j。
57.对比例
58.(1)渗碳处理:采用强渗和扩散工艺对20crmnti主轴进行表面渗碳,渗碳温度为925℃,强渗碳势为1.20%,渗碳时间为10h,扩散的碳势为0.9%,扩散时间为4h。
59.(2)淬火处理:渗碳完成后,随炉冷却至850℃,出炉油冷至室温,油温为50℃。
60.(3)时效处理:深冷处理后的20crmnti主轴进行精加工处理后,放入时效热处理炉中进行时效处理,加热温度为50℃/h,时效温度为200℃,保温时间为8h,随后出炉空冷至室温。
61.本对比例经过最终处理后,对表面进行含碳量检测和洛氏硬度测试,在心部取样加工成标准室温拉伸试样和夏比v口冲击试样。测试结果表明,经过本对比例的热处理后,20crmnti主轴的表面含碳量约为0.95wt%,渗碳层厚度为1.40mm,表面硬度为61hrc;心部材料抗拉强度达到1150mpa,室温冲击功仅为33j。
62.图4为实施例1与对比例样品表面xrd检测结果,对图4进一步分析,检测残余奥氏体含量如图5所示,可见深冷处理后样品中残余奥氏体含量明显低于传统工艺处理样品。进一步通过实施例1-4与对比例发现,未经深冷处理样品表面硬度低,心部材料抗拉强度也较低,而室温冲击功远低于深冷处理样品。
63.最后应说明的是:以上所述仅为本发明的优选实施例而已,并不用于限制本发明,尽管参照前述实施例对本发明进行了详细的说明,对于本领域的技术人员来说,其依然可以对前述各实施例所记载的技术方案进行修改,或者对其中部分技术特征进行等同替换,凡在本发明的精神和原则之内,所作的任何修改、等同替换、改进等,均应包含在本发明的保护范围之内。